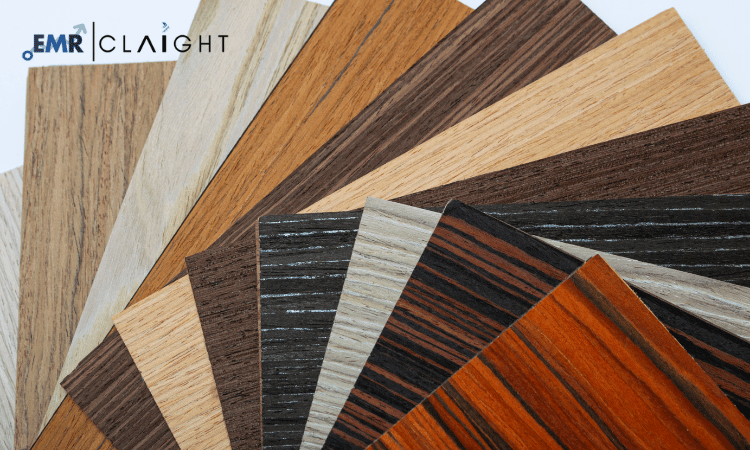
Decorative laminated sheets, commonly known by the brand name Sunmica, are widely used in interior design and furniture applications for their aesthetic appeal, durability, and versatility. These sheets provide an elegant and protective finish to surfaces, making them ideal for residential, commercial, and industrial projects. With the increasing demand for stylish and functional interior solutions, establishing a decorative laminated sheets manufacturing plant presents an excellent business opportunity. This article delves into the essential aspects of setting up such a plant, exploring raw materials, production processes, equipment, and market potential.
Overview of Decorative Laminated Sheets (Sunmica)
Decorative laminated sheets are composite materials made by fusing multiple layers of paper or fabric with resins under high pressure and temperature. The top layer is usually printed or coated with a decorative design, while the core layers provide strength and stability. These sheets are available in various textures, colours, patterns, and finishes, catering to diverse design preferences. Known for their resistance to scratches, stains, and moisture, laminated sheets are extensively used for furniture, countertops, wall panels, and cabinetry.
Get a Free Sample Report with Table of Contents@ https://www.expertmarketresearch.com/prefeasibility-reports/decorative-laminated-sheets-sunmica-manufacturing-plant-project-report/requestsample
Key Components of a Decorative Laminated Sheets Manufacturing Plant
- Raw Material Procurement
The primary raw materials include craft paper, decorative paper, resin (phenolic and melamine), and additives. Sourcing high-quality raw materials is essential for ensuring the durability and aesthetic quality of the final product. - Machinery and Equipment
Advanced machinery is crucial for efficient production. Key equipment includes:- Impregnation Machines: For saturating paper with resin.
- Dryers: To remove excess moisture from impregnated paper.
- Hydraulic Presses: For laminating the layers under high pressure and temperature.
- Cutting Machines: To trim the sheets to standard sizes.
- Polishing Units: For achieving a smooth and glossy finish.
- Packaging Machines: For securely packing the sheets for storage and transportation.
- Plant Layout and Design
A well-organised layout ensures smooth workflow and efficient operations. The plant should have separate areas for raw material storage, impregnation, pressing, finishing, and packaging, along with adequate ventilation and dust control systems. - Utilities and Infrastructure
Reliable utilities such as electricity, water, and climate-controlled storage are essential. Adequate waste management systems should also be in place to handle resin waste and other by-products responsibly. - Workforce and Training
Skilled personnel are required to operate machinery, oversee production, and ensure quality control. Regular training ensures workers are proficient in maintaining safety and efficiency standards.
Manufacturing Process of Decorative Laminated Sheets
The production of decorative laminated sheets involves several stages to ensure a high-quality, durable product:
- Impregnation
Kraft paper and decorative paper are impregnated with phenolic and melamine resins, respectively, to enhance their strength and resistance to moisture and heat. - Drying
The impregnated papers are passed through dryers to remove excess moisture and achieve the desired resin content. - Stacking and Assembly
Layers of impregnated kraft paper (core) are stacked together with a decorative paper layer on top. A protective overlay may be added for extra durability. - Laminating
The stacked layers are placed in hydraulic presses, where they are subjected to high pressure and temperature. This process fuses the layers into a single sheet with a uniform thickness and finish. - Trimming and Finishing
The laminated sheets are trimmed to standard sizes and polished to achieve the desired texture and gloss level. - Quality Testing
The finished sheets undergo rigorous testing for parameters such as thickness, surface finish, and resistance to scratches and stains. - Packaging
The final product is packed securely to prevent damage during storage and transportation.
Applications of Decorative Laminated Sheets
Decorative laminated sheets are used in various applications due to their versatility and aesthetic appeal:
- Furniture: Widely used for tabletops, cabinets, and wardrobes.
- Wall Panels: Enhances the look of interiors in residential and commercial spaces.
- Countertops: Ideal for kitchens and bathrooms due to their moisture resistance.
- Doors: Provides a stylish and durable finish for doors.
- Retail Displays: Used in creating attractive retail shelving and displays.
Market Potential and Demand Drivers
The demand for decorative laminated sheets is driven by several factors:
- Growing Construction and Interior Design Industry
Rapid urbanisation and increasing investments in infrastructure and real estate boost the demand for decorative materials. - Aesthetic Preferences
Consumers’ growing focus on stylish and personalised interiors fuels the demand for a wide range of patterns and finishes. - Durability and Low Maintenance
The durability, cost-effectiveness, and ease of maintenance of laminated sheets make them a preferred choice over traditional materials like wood and veneer. - Sustainability Trends
The use of eco-friendly resins and recycled materials in laminated sheet production aligns with consumer demand for sustainable products.
Challenges in Decorative Laminated Sheets Manufacturing
- Raw Material Costs
Fluctuations in the prices of paper and resin can impact production costs. Long-term supplier agreements can help mitigate this risk. - Quality Control
Ensuring consistent quality across batches requires advanced testing equipment and stringent quality control measures. - Environmental Compliance
Adhering to environmental regulations for emissions and waste disposal is essential for sustainable operations. - Competition
The market is competitive, with numerous players offering similar products. Differentiation through innovation and quality is crucial.
Sustainability in Decorative Laminated Sheets Manufacturing
Sustainability is becoming a key focus in the laminated sheets industry. Key initiatives include:
- Eco-Friendly Resins: Using resins with low volatile organic compounds (VOCs) to reduce environmental impact.
- Waste Management: Recycling production waste and responsibly disposing of non-recyclable materials.
- Energy Efficiency: Implementing energy-saving technologies in production processes.
- Sustainable Sourcing: Procuring paper and other materials from responsibly managed sources.
Key Success Factors for a Decorative Laminated Sheets Manufacturing Plant
- High-Quality Standards: Maintaining consistent quality and compliance with industry standards builds trust and customer loyalty.
- Product Innovation: Offering unique textures, patterns, and finishes to cater to diverse consumer preferences.
- Operational Efficiency: Streamlining production processes and investing in advanced machinery enhances productivity and reduces costs.
- Effective Marketing: Highlighting the durability, aesthetics, and eco-friendly aspects of the product through targeted campaigns increases visibility and demand.
- Sustainability Practices: Adopting eco-friendly measures strengthens brand reputation and aligns with global trends.
By focusing on these factors, a decorative laminated sheets manufacturing plant can successfully cater to the growing demand for innovative and durable interior solutions while ensuring sustainable and profitable operations.